Shaping careers in plastic fabrication
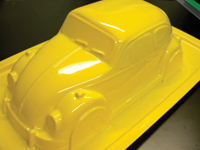
We live in a high-technology world, where plastics materials are used extensively in almost every aspect
of our lives. The New Zealand plastics industry now has an annual turnover of $2.6 billion and employs 8000 people. Virtually everything we touch and see is made from plastics.
Plastics materials are clean, energy efficient, strong, lightweight, cost-effective and, more importantly, can be recycled and re-used.
Plastic fabrication and repair can be carried out on almost all thermoplastics. Plastics can also be bent or formed into almost any size or shape.
Plastics materials are processed by a range of manufacturing technologies – and today all of these can be employed in educational institutions.
Common examples of this equipment would include: vacuum forming machinery, plastic fabrication and repair welding equipment, plastic sheet bending equipment, injection moulding equipment, styro-cutters, hot knives, dome formers and plastic dip coating.
To give you some idea of the scope of where plastics technologies are being used let’s consider one market:
Automotive repair
Just as one example, plastics are being used extensively in the manufacture of automotive panels and fixtures. Today the average motor vehicle has over 350 kilograms of plastic on board, all of which can be welded. Bumper bars, grilles, headlight housings, fluid bottles, radiators and even engine parts are today being manufactured in plastic.
And with fuel economy being extremely important, we are likely to see the use of plastics in this field increase dramatically.
Strong, structural welding is possible, using a ‘hand-held’ plastic welding tool, which can be purchased for as little as $700. Not bad when you consider the comparable costs of say metal welding equipment, or perhaps a wood turning lathe – and the skills and techniques required for welding plastics are very easy to learn. This single industry sector continues to expand. Vehicle smash repairers are rapidly moving into plastics repairs –
1. Plastic parts can take some time to be delivered. Repairing the parts means faster turnaround, improving customer service. And repair benefits the environment.
2. With the skills learned in welding plastics students have a service to offer other repairers.
3. Most importantly, all the profits from the plastic repair go directly to the repairer.
This is just one example of a career prospect in plastics. Many other industries are today working and welding plastics. Other industries include: tarps and banner manufacture, tank fabrication, lining of landfill sites, pond lining, vinyl floor welding, welding of roofing membranes, pipeline welding – and the list goes on. If your school technology department is still dealing with only wood and metal, now is the time to get into plastics technology. While some have already developed good plastics technology centres in their schools, many are still well behind, which will not provide students with the benefits of work and career opportunities in the plastics sector.
Whether you use a hand-held plastic welding tool or a vacuum former, these technologies are the future – get plastic technology into your school.