Fume cupboards must be maintained to safety Standard
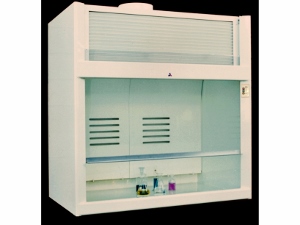
The Building Act 2004 uses laboratory fume cupboards as an example of equipment, which must be included in the compliance schedule for building warrant of fitness. This means that the building owner is responsible to have scheduled items tested and certified annually. For fume cupboards the reference Standard for testing is AS/NZS2243.8 Safety in Laboratories: Part 8.
State schools are owned by the Ministry of Education, and operated by the Board of Trustees. As owners, the Ministry contracts out compliance testing, including fume cupboards. These contracts are price driven, which has a limiting effect on the scope of testing. In general they follow a short checklist for testing airflow and some aspects of compliance. No maintenance is performed. Very few auditors have any real knowledge of construction or operation of fume cupboards, and may not even know enough to identify a defect, let alone report or fix it.
The problem is that the client sees a sticker on the fume cupboard and thinks it means the fume cupboard has been maintained. To make it worse, the Form12A submitted to the local authority with the BWOF declares that the item performs and has been maintained to the Standard even though usually this is not true.
Standard AS/NZ 2248.8 does not require maintenance to be done when a fume cupboard is tested, but DOES require testing as part of the maintenance plan. So the auditors are not required to carry out any maintenance themselves. However, they ARE required to determine compliance with maintenance as per section 5 of the Standard. If the auditor is not maintaining the unit themselves, they must seek proof of maintenance by others … but no auditor ever does, and so by negligence the client is misled.
The Ministry will not maintain equipment. Maintenance is the responsibility of the school administration. Fume cupboard maintenance is not difficult, but does require a trained eye to assess construction and operational condition. Expertise and experience are worthwhile.
Now, I would like to address the issue of age. Fume cupboards are audited to the Standard that was current at the time of installation. There are still many fume cupboards around which were installed before 1986, when the first Standard was published. Therefore these fume cupboards do not have any conditions of compliance at all. The products of this era are very poor, and have significant deficiencies compared with current models. They are supposed to be safety equipment, but would be declared UNSAFE by today’s Standard. The main deficiencies are insufficient airflow, poor airflow distribution in the fume chamber (letting fumes escape into the lab), poor lighting, lack of spill protection, absence of safety sequence control, and poor fume dispersal. It is not practical or cost-effective to modify these old fume cupboards, and anything over 20 years old owes nothing on the books. However, there is no incentive to replace them because they continue to get a “granny” exemption sticker every year.
Fume cupboards are safety equipment for which our expectations have advanced, along with our statutory liability towards our employees. I do not think any board would allow students to go to school in a 40-year-old bus with no speedo, brakes, seatbelts or lights, but that is the equivalent hazard exposure in old laboratories. That fume cupboards are a nominated example in The Building Act is proof of their statutory importance as safety equipment, but because of this loophole granny exemption, many pupils and staff are still exposed to the harmful inadequacies of ancient defective fume cupboards.
Malcolm Hubbert an engineer with 38 years’ experience in designing, manufacturing, installing and repairing fume cupboards, serves on the committee which wrote the AU/NZ Standard for fume cupboards, and is a registered Independent Qualified Person for auditing fume cupboards.